The Science of Air: Installing Modular Structures in Manufacturing Facilities
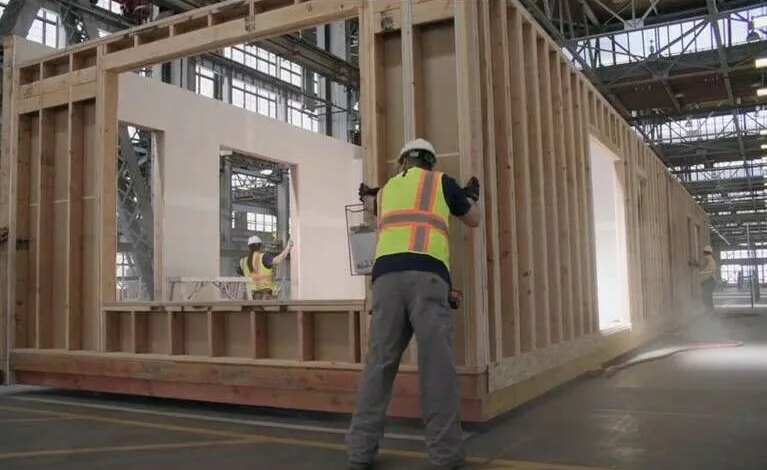
Paul Jakse, VP Sales for industrial solutions supplier AeroGo explains how largely redundant hovercraft transport technology is being used to resolve obstacles to erecting modular structures within factories.
Construction of modular structures in many manufacturing facilities has historically proven challenging, especially the material handling process. Space available tends to be too restricting and the modular units (or “boxes”) too large for cranes and other movement tools. It’s a major struggle even for rails and steel rollers to safely relocate long structures or full assemblies in these environments.
One Colorado-based manufacturer of modular single-family homes knows these challenges all too well. The company wanted to build a more productive facility and had to find a different approach for navigating the assembly line. The firm’s goals were ambitious—it wanted to produce more than 700 homes, apartments, and townhomes annually. To maximize efficiency and productive capacity, the company recognized the need for an innovative workflow: a high-efficiency, U-shaped assembly line surrounding a mezzanine complete with tooling, parts, and offices capable of surveying the entire production line from above.
Typical material handling systems would limit flexibility and inhibit their ability to design such a high-performance workflow, however. The company, like so many of its peers, looked for another answer and found it in air casters.
The science of air casters
Air casters are a low-profile material handling system that easily slides under modular boxes in these manufacturing facilities. The casters use compressed air to inflate donut-shaped bags under each multi-ton box, effectively transforming each into a giant hovercraft that floats on a nearly frictionless film of air that requires less than 1-kg. of force to move 1,000-kg units. A small team of no more than half a dozen workers—four movers and two spotters—can easily move an entire box home just by pushing it. All air caster systems enable users to lift and move structures of any size and shape in a precise manner in any direction, including rotating in place.
Why air casters?
First, air casters eliminate problems that can slow or stall production. The sheer flexibility of air casters also appealed to a California-based manufacturer of multifamily housing. That operation must move massive, 30,000-lb. module boxes through a 30-workstation assembly line quickly without disrupting the rest of the production process. With typical material handling solutions, such high-efficiency workflows are often vulnerable to even minor delays or mishaps that can cause the entire production line to grind to a halt until an issue is resolved.
Air casters offer the necessary flexibility to keep the line moving. Operations like these simply move the module out of the primary line, turn it sideways, and set it aside for later insertion into the production line. By contrast, a material handling system that requires permanent installation, like rails or cranes, tends to limit or eliminate flexibility.
Second, air casters can also increase overall efficiencies. Air casters can move so quickly that a small team of operators can move even a house-sized box from one station to the next in as little as a few minutes. Because they are so maneuverable, the casters are capable of precision placement, even if structure rotation is required.
Air casters’ flexibility also allows for improved facility layouts that can increase productive capacity. For example, manufacturers can turn a straight-line production into a U-shape very easily. That allows facilities like the Colorado builder to maneuver down a certain number of stations in one direction, move laterally and return across the same number of stations effectively, effectively doubling the number of boxes under construction at any time.
Third, air casters enable manufacturing plants to accommodate changes seamlessly. Modular manufacturing plants must accommodate changes regularly. An operation might have been designed to produce 56-foot boxes, only to later need either alternate or additional production of 76-foot boxes. A material handling system like rails or even steel rollers would make it prohibitively difficult and, in many cases, impossible to accommodate such changes. With air casters, everything is fluid and changeable.
Altogether, air casters eliminate friction points that slow modular production. Modular, prefabricated construction technologies can produce high-quality buildings economically and quickly, provided they utilize flexible, low-cost, and efficient tools. For material handling, air casters easily float to the top of the tool list and have fast become the preferred solution for the modular construction industry.
The bottom line: expect air caster-based systems to play a growing role in modular construction thanks to their flexibility, ease of use and cost-effectiveness.